Table of Content
Winsor Homes is owned and operated by the Winsor Family since 1973. What are you doing all the way down here at the bottom of the page? Oh, you're still a bit nervous if a custom-modular home is for you? That's why we want to extend our personal offer to come by our showroom and talk about the process, the designs, the options. You'll leave better informed and with a handshake (or more likely, a hug. It seems to happen all the time).
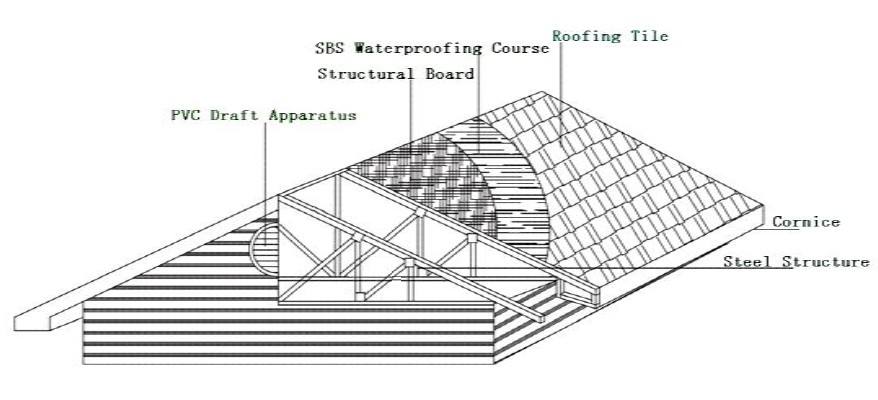
Everything is fully customizable, from the house length to the kitchen configurations, so go ahead and tell them what you’d like your home to look like. If you are looking to have a modular home constructed for your New Hampshire home site, get in touch with us anytime. Excavator will excavate foundation and create driveway; install septic system, grade disturbed areas, and spread loam. The homes conduct heat and electricity with expanded efficiency, and they also provide vapor permeability and decreased external noise conductivity.
Plans and Pricing
Passive House designs use 90% less energy than conventional homes, which is a major advantage in building home equity, paying off your loan, and supporting ecological efforts. Build with Nature specializes in passive designs for ultra-low energy usage in homes and buildings. Solsken by Ecocor is a construction company that specializes in building energy-efficient buildings and homes in North America.

The reputation of the company speaks for itself as one of the best-known fabricators of luxurious homes. Dvele advertises that you can choose a home template and customize your home in less than 10 minutes, but you probably need to have a clear vision of what you want. Using Impresa Modular ensures better management of materials and resources that are stored in protected warehouses to prevent damage and deterioration.
The set includes:
The latter choice runs $417,999 and features remote control operations, advanced HEPA air quality control, ITC certification, and 99.9% antivirus and anti-bacterial protection. The company also features singular ways to personalize your space. Deltec Homes range in price from $250 to $500 per square foot. The costs of homes run about $237 per square foot, and the company has been in operation for more than 10 years.
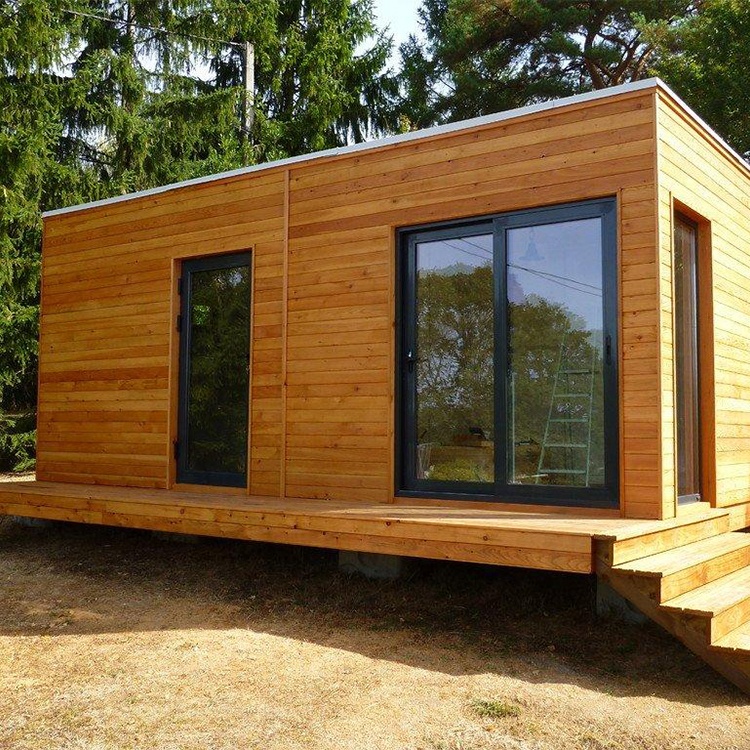
Pratt Homes offers an incredible range of home design options and customizations that make your home unique. The second phase consists of signing the purchase agreement and developing detailed floor plans. The third phase consists of fabricating the components, shipping them to your site, and assembling your home.
What’s Typically Not Included in the Cost
The general rule is that prefab building is cheaper than traditional construction by 10% to 25%. Most of the site prep, foundation, and building permit fees would apply equally to building a new home, so these extra expenses should not be added to your totals for comparisons. Your cost of labor usually drops in prefab housing, which is another reason to exclude extra expenses from comparisons. Location affects the price of your prefab home more than any other single factor. Depending on where you decide to build, the cost of your prefab kit varies considerably.

The smallest ranch-style home starts at $136,600 for 1,100sqft, while the largest is $201,500 for 2,155sqft. Did you know that prefab homes are the most popular in New Hampshire , with Maine in the close second? Overall, the entire New England region is big on manufactured homes.
If you are conscious of these spaces, you’ve found your match. The Company produces homes in various styles, including capes, colonials, ranches, vacation homes, and multi-family units. Check out their plans, including ranch homes, cape-style, and two-story colonial homes. Casey Modular Homes is a good choice for fast and affordable housing in New England. The Hillsboro business has already completed hundreds of projects across the region. The company can also cover additional costs for site excavation, foundation, and land development.

Wolf Industries is a full-service construction company based in Washington, with projects around Oregon, Idaho, Utah, and California. It specializes in prefab accessory dwelling units and tiny modular homes. 3 bedroom Ranch Home, quality built, includes delivery, crane & set, roofing and siding completed. Go Logic embraces Passive House principles of using prefab components to speed construction and reduce costs.
The walls, roofs, and floors are made from Structural Insulated Panels with excellent strength and thermal resistance. This digest will show you the top manufacturers of all types of tiny homes in many states and around the world. Well company will drill well, install pump and pressure tank and bring water line into basement.
Millions of people ask HomeGuide for cost estimates every year. We track the estimates they get from local companies, then we share those prices with you. Certain design limitations exist since contractors must move the modules onto a truck for delivery. You often need to own or buy a piece of land before installing the modular home. Additions such as a garage, basement, or deck add to your overall cost. Prices depend on the size and whether it's attached to the home or not.
The average cost to build a stick-built house is $100 to $200 per square foot. Modular home prices range from $80 to $160 per square foot on average. The average cost to move an off-frame modular home is $5,000 to $15,000 depending on the size, permits, distance, and set-up complexity. Moving an on-frame manufactured home costs $1,000 to $8,000 for up to 50 miles, depending on if set-up services are included after relocating.

Features of these homes include panelized walls, roofs, and flooring components that speed up the building process and reduce costs. The company also offers an age-in-place system for people who expect to live in their homes for a lifetime. Homes in this category are designed with building flexibility to expand, downsize, add automation features, etc.
Kent offers more than 100 customizable floor plans ranging from 600 to 2,500 square feet. By building in a factory, quality is controlled throughout the process, much better than can be managed with onsite, outdoor construction. Couple the quality of modular construction with its design flexibility and it is an unbeatable combination when choosing to build a custom home. It can be a ski chalet overlooking the slopes at Gunstock Mountain, it can be a cabin tucked away on the Androscoggin River, a cozy cottage in Hanover, or any style in between.
The cost of custom design prefabricated homes runs higher than standard models — about $100 to $250 per square foot. After all installation, site work, and finishing touches are added, the total cost of a custom home runs between $200,000 and $500,000. Requesting a custom design is a relatively painless process because most modular builders willingly incorporate your design suggestions into the modular home blueprints. Custom modular home prices range from $100 to $250 per square foot or between $200,000 and $500,000 when including all site-work, installation, and finishing. Most modular builders will customize their existing designs to change the finishes, floor plan, or the home's size. The average modular home costs $50 to $100 per square foot for delivering the base unit, or between $80 and $160 per square foot total with site prep, installation, and finishing.
No comments:
Post a Comment